News JVTech The US has just solved a very expensive problem with its F-35 fighter jets. All it took was some plastic and a 3D printer
A popular hobby for millions of people around the world, 3D printing is an area that is also of interest to many professional sectors. The US Army in particular has found a way to use it to make serious savings.
For an individual, buying a 3D printer capable of printing plastic or resin objects is not very expensive. And some advocate the environmentally responsible interest of the approach, since by printing certain parts it is possible to repair some everyday items that would otherwise end up in the bin.
Now imagine such logic applied in a sector where the smallest repair can cost a fortune. Incidentally the aviation, and more precisely the army. A sector where it is not only about economics, but still: lowering costs is always good to take!
When the best solution is far from the most expensive
The Air Force Repair Improvement Program (AFREP) is not the most high-profile department in the US militaryand still, it has a strategic role in the maintenance of combat aircraft. It is one of the most efficient departments, but also the most profitable, not for what it manages to produce, but for what it manages to save.
The engineers and technicians who work there have the heavy task of finding solutions for repairs, replacing parts that have been unavailable for a long time or even finding alternatives whose costs do not increase the budget. And sometimes the most effective solution is far, far from the most expensive.
The proof: in 2017, at the Mountain Hope base in Idaho, officials had resigned themselves to throwing away a power supply that was considered beyond repair. Price per piece: $20,000. This is where AFREP technicians came in to find a solution. After studying the part, they found a way to fix it using a simple $5 resistor. “It’s like fixing a $300 smartphone with a part that costs 8 cents”, summed up a US Army sergeant major at the time.
Of course, to get there, a lot of reverse engineering was needed. But the game was worth it as potentially millions of dollars have been saved.
3D printing for fighter aircraft repair
Sometimes the parts suitable for a repair do not exist as such. For the F-35 stealth fighter, AFREP engineers had to go even further to overcome a breakdown that is as frequent as it is costly., attached to the sensors in the nose of the aircraft. In practice, these very fragile sensors must be protected from dust and moisture as soon as the planes are on the ground. But these protective parts are also difficult to handle, as their fasteners tend to break easily. Problem: these are items that cost $600 each! Their replacement quickly costs the army a fortune.
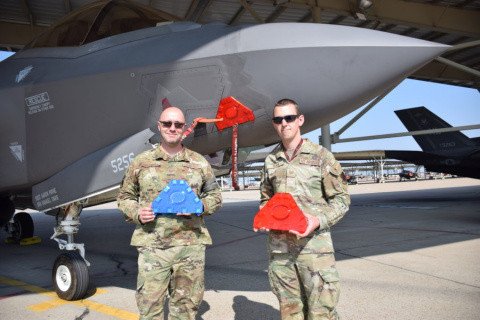
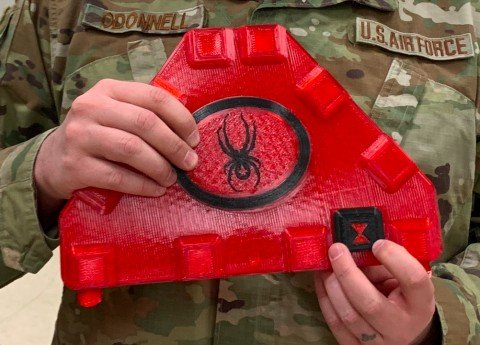
AFREP therefore looked for alternatives. IN an article published on Air & Space Forces MagazineStaff Sergeant Christopher O’Donnell explains it the goal was to go as simple as possible, and the solution was found on the side of 3D printing. It is a rubber-like metal sheet that is printed in a shape that fits the sensors. Combined with magnets and an O-ring, it stays in place and is weatherproof.
Cherry on the cake: each piece takes just 22 hours to print and costs $45, compared to $600 for the base piece.
Very proud of his find, Christopher O’Donnell is now receiving many inquiries from other F-35 bases seeking these valuable parts.. Enough to give ideas to other people in the army, but also to civilians looking for a solution to repair items if spare parts are missing. What if you switched to 3D printing?